Welcome to JZT Molds
Precision Molds, Perfect Parts – Shaping the Future of Manufacturing
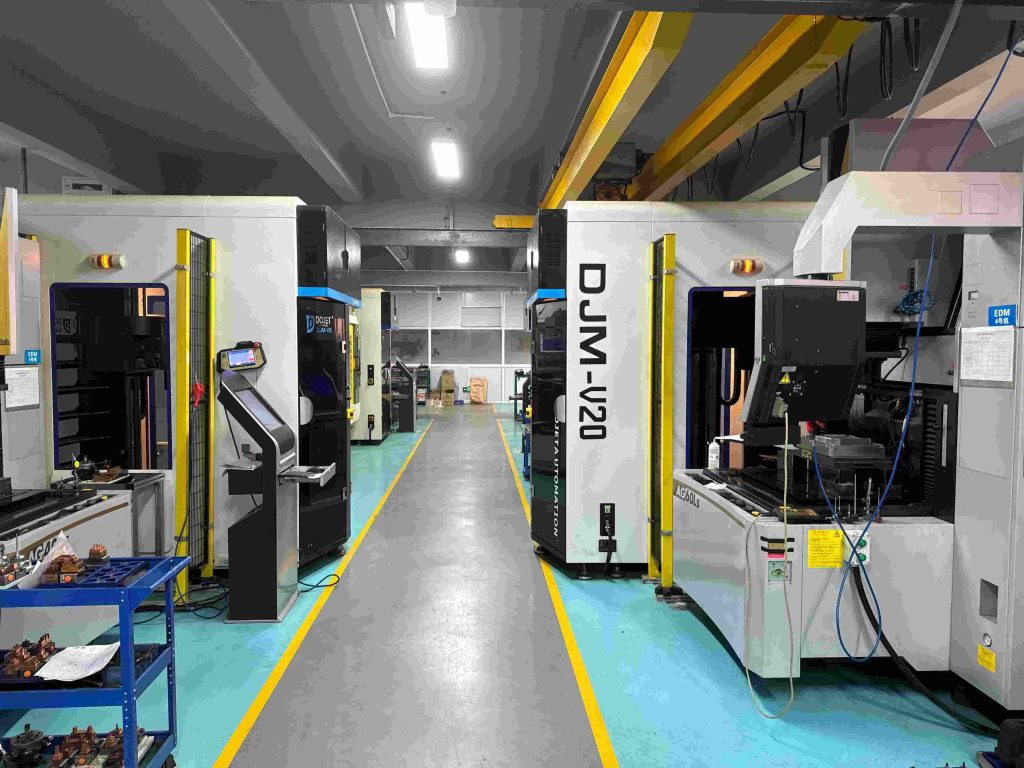
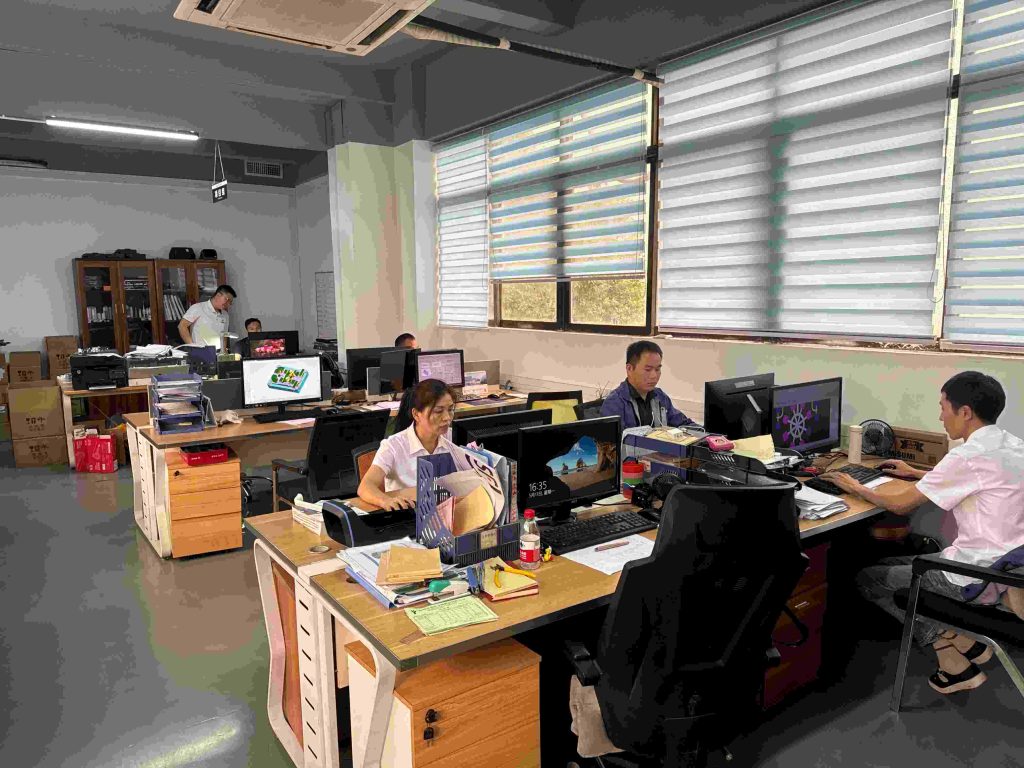
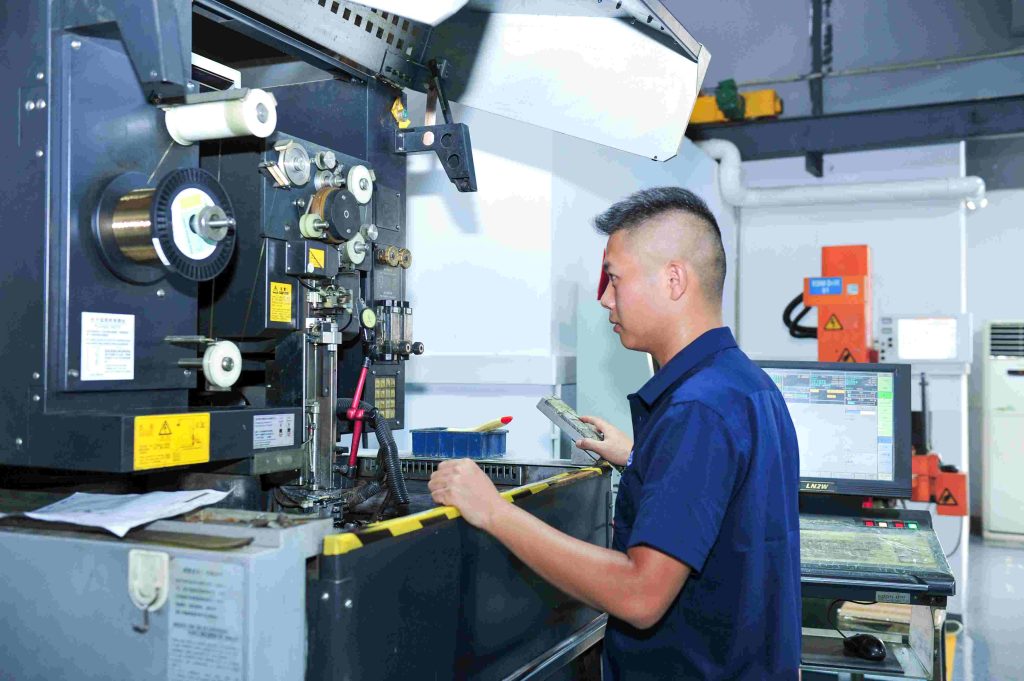
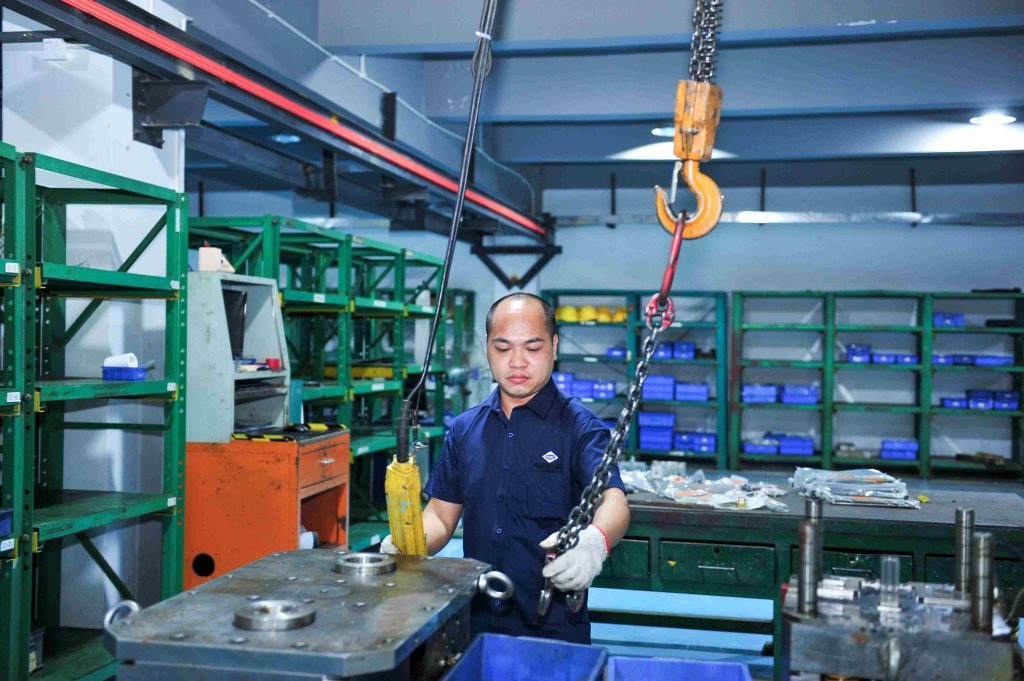
What Are Plastic Injection Molds?
Plastic injection molds are essential tools used to produce plastic parts by injecting molten plastic into a mold. They are used across various industries including automotive, medical, and consumer goods.
Key Features & Benefits
- Precision Engineering: Accurate molds for complex designs.
- Durable Construction: Long-lasting materials for extended use.
- Customization: Tailored to your specific industry needs.
- Cost-effective Production: High-volume manufacturing with minimal waste.
Advanced Technology & Customization Capabilities
Material Options
Choosing the right material for your plastic injection mold is crucial as it directly impacts the durability, cost, and performance of the final product. At JZT, we offer a variety of high-quality materials tailored to meet your specific needs.
Aluminum
Lightweight and Durable
Aluminum molds are an excellent choice for industries where speed and cost-efficiency are priorities. The lightweight nature of aluminum allows for faster machining, reducing production time and costs significantly. Despite being lighter, aluminum offers remarkable durability and can withstand the rigors of short to medium production runs. These molds are particularly suitable for prototyping and low-volume production where quick turnaround and flexibility are essential.
Advantages:
- Faster Production: Due to its softer nature, aluminum can be machined more quickly than steel, allowing for faster mold creation.
- Cost-Effective: Lower material and machining costs make aluminum molds more affordable, especially for short runs.
- Good Heat Dissipation: Aluminum has excellent thermal conductivity, which helps in reducing cycle times by allowing the mold to cool faster.
Best Use Cases:
- Prototypes: Ideal for creating initial prototypes or small-batch production where adjustments may be needed.
- Consumer Goods: Perfect for products with a shorter life cycle or those requiring frequent design changes.
Steel
Ideal for High-Volume Production
Steel is the most commonly used material for plastic injection molds, particularly for high-volume production runs. Its strength and durability make it the preferred choice for molds that need to produce millions of parts over their lifespan. Steel molds are highly resistant to wear and tear, ensuring consistent quality throughout the production cycle. The hardness of steel also allows for the creation of more intricate and detailed designs, making it suitable for complex parts that require high precision.
Advantages:
- Durability: Steel molds can withstand high pressures and are resistant to abrasion, making them ideal for long-term use.
- Precision: The hardness of steel allows for detailed and complex mold designs, ensuring high-quality outputs.
- Longevity: Steel molds can be used for millions of cycles without significant wear, making them cost-effective in the long run.
Best Use Cases:
- Automotive Parts: Ideal for producing large volumes of intricate and durable components.
- Medical Devices: Suitable for high-precision parts that require stringent quality standards.
- Industrial Components: Perfect for heavy-duty applications where durability and accuracy are crucial.
Special Alloys
For Specific Industry Requirements
For industries that demand exceptional performance or have unique production needs, special alloys offer a tailored solution. These materials are engineered to provide specific properties such as enhanced corrosion resistance, higher strength, or improved thermal conductivity. Special alloys are often used in industries where the standard materials might not perform well under extreme conditions or where the parts produced have to meet very strict regulatory requirements.
Advantages:
- Enhanced Properties: Special alloys can be customized to provide superior properties such as resistance to extreme temperatures, corrosion, or chemical exposure.
- Specialized Applications: These alloys are often necessary for producing parts used in harsh environments or that need to meet strict regulatory standards.
- Improved Performance: The unique properties of special alloys can lead to better performance and longevity of both the mold and the parts produced.
Best Use Cases:
- Aerospace Components: Used where materials must withstand extreme conditions without degrading.
- Medical Implants: Ideal for parts that require biocompatibility and resistance to body fluids.
- Chemical Processing Equipment: Suitable for molds used in producing parts exposed to corrosive chemicals or high temperatures.
Customization Process
At JZT, we understand that every project is unique, requiring a tailored approach to ensure the final product meets all specifications and performance criteria. Our customization process is designed to guide you from concept to completion, ensuring that your plastic injection mold is perfectly suited to your needs. Here’s a detailed look at each step in our process:
1. Design Consultation
The customization journey begins with a thorough design consultation. This stage is crucial as it lays the foundation for the entire project. During the consultation, our team of experts works closely with you to understand your specific requirements, including the intended application of the mold, production volume, material preferences, and any particular challenges that need to be addressed.
Key Aspects of Design Consultation:
- Needs Assessment: We discuss your project’s goals, including the desired product characteristics, production environment, and performance requirements.
- Feasibility Analysis: Our engineers assess the technical feasibility of your design, considering factors such as material selection, mold complexity, and potential production challenges.
- Preliminary Design Concepts: Based on your input, we provide initial design concepts that align with your objectives, ensuring that all critical aspects are covered before moving forward.
Outcome:
- A clear understanding of your project requirements.
- A preliminary design concept that meets your goals and expectations.
2. CAD Modeling
Once the design consultation is complete, we move on to CAD (Computer-Aided Design) modeling. This step involves creating a detailed 3D model of the injection mold using advanced CAD software. The model serves as a digital prototype, allowing for precise visualization and refinement of the mold design before any physical production begins.
Key Aspects of CAD Modeling:
- 3D Visualization: We create a comprehensive 3D model of the mold, allowing you to see exactly how the final product will look and function.
- Detailed Design Refinements: Our engineers fine-tune the design, optimizing features such as mold cavities, cooling channels, and ejection systems to ensure maximum efficiency and quality.
- Simulation and Analysis: Using the CAD model, we perform simulations to predict the mold’s performance under various conditions, identifying and addressing potential issues early in the process.
Outcome:
- A finalized 3D model of the mold, ready for prototyping.
- Confidence in the mold’s design and functionality, backed by thorough analysis.
3. Prototyping
With the CAD model finalized, the next step is prototyping. This involves creating a physical prototype of the mold or the parts it will produce, allowing for hands-on evaluation and testing. Prototyping is a critical phase as it provides the opportunity to make adjustments and improvements before full-scale production begins.
Key Aspects of Prototyping:
- Rapid Prototyping: We use advanced techniques such as 3D printing or CNC machining to quickly produce a prototype, saving time and reducing costs.
- Functional Testing: The prototype is tested under real-world conditions to evaluate its performance, durability, and overall quality.
- Iterative Improvements: Based on the results of the testing, we make any necessary modifications to the design, ensuring that the final product will meet all specifications.
Outcome:
- A fully functional prototype that can be tested and evaluated.
- Iterative improvements leading to a design that is optimized for production.
4. Final Production
After the prototype has been tested and refined, we proceed to final production. This stage involves the manufacturing of the injection mold at scale, using the materials and specifications agreed upon during the previous stages. Our state-of-the-art facilities and stringent quality control processes ensure that every mold we produce meets the highest standards of precision and durability.
Key Aspects of Final Production:
- High-Precision Manufacturing: We use the latest equipment and technology to produce molds with exceptional accuracy and consistency.
- Quality Assurance: Every mold undergoes rigorous quality checks at each stage of production, including dimensional inspections, material testing, and performance evaluations.
- On-Time Delivery: We manage the entire production process efficiently to meet your deadlines, ensuring that your molds are delivered on time and ready for use.
Outcome:
- A high-quality injection mold that is ready for mass production.
- Confidence in the mold’s ability to perform reliably and efficiently in your manufacturing process.
Applications Across Multiple Industries
Automotive
Precision Components: JZT molds are ideal for manufacturing complex automotive components such as engine parts, interior trims, and exterior panels. These molds ensure that every piece meets the strict tolerances required by the automotive industry.
High Durability: Our molds are built to withstand the high stress and repetitive use common in automotive production environments, ensuring long-lasting performance and reduced downtime.
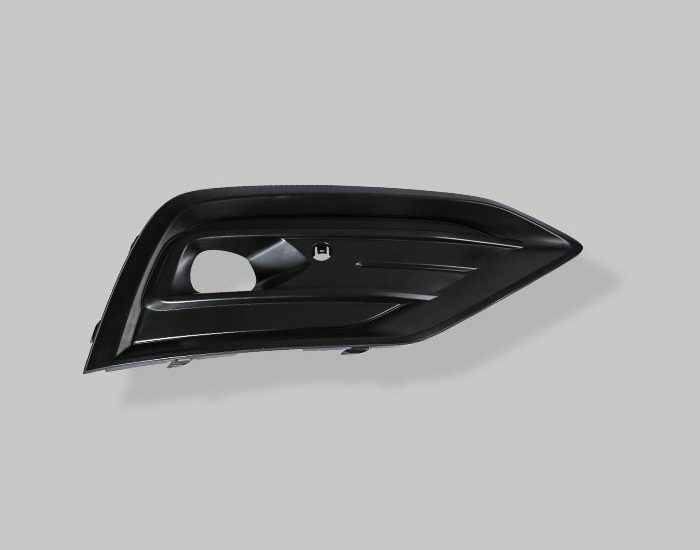
Medical
Precision and Reliability: JZT molds are crafted to meet the exacting standards of the medical industry, ensuring that every component produced is precise, reliable, and consistent, which is critical for medical applications.
Support for Complex Designs: Our expertise in mold design allows us to create molds for intricate medical devices and components, supporting the production of highly detailed and accurate parts necessary for the healthcare sector.
Material Versatility: We provide molds that can work with a variety of materials commonly used in the medical industry, ensuring that your products meet the necessary durability and performance requirements.
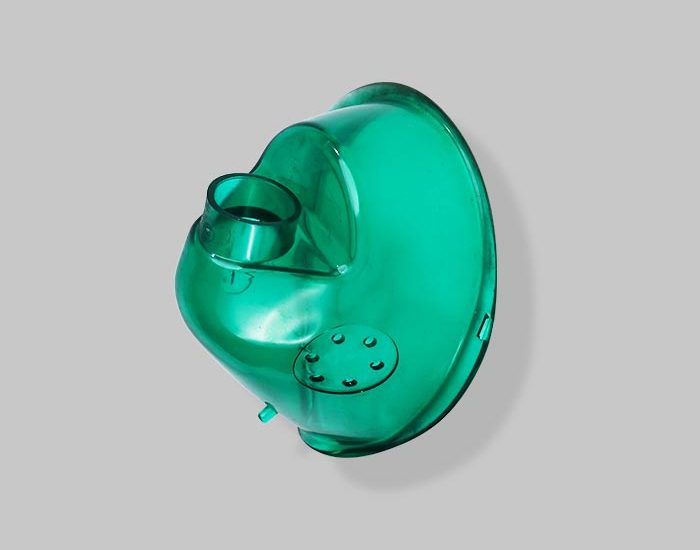
Consumer Goods
High-Volume Production: Our molds are optimized for high-volume production, ensuring consistent quality and fast turnaround times for consumer products ranging from household items to electronics.
Versatile Applications: Whether it’s for durable goods or disposable items, JZT molds can be customized to suit a wide variety of consumer product applications, ensuring flexibility and efficiency in production.
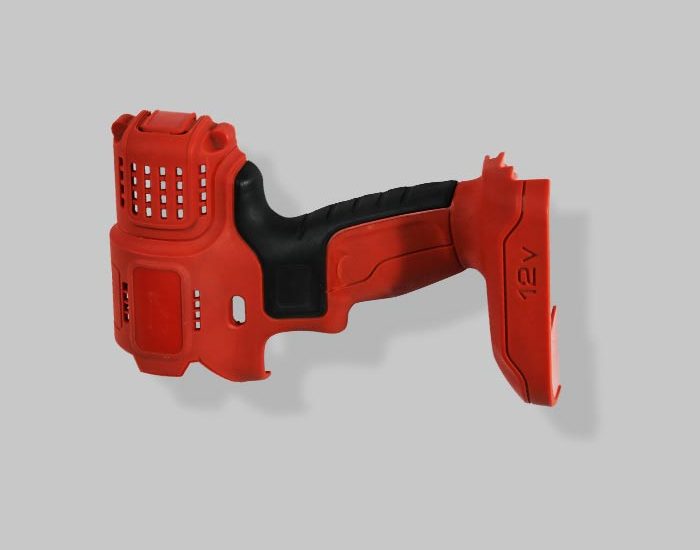
Why Choose JZT for Your Plastic Injection Molds?
At JZT, we pride ourselves on delivering high-quality plastic injection molds using top-tier materials and advanced machinery, ensuring precision and durability at competitive prices. Our 24/7 customer support and expert consultations provide personalized guidance to meet your specific project needs. With global reach, our molds comply with international standards, and our reliable shipping ensures timely delivery worldwide.
GET IN TOUCH
Whenever you need us, we’re here for you.
Ready to discuss your molding needs? We are here to help you every step of the way.
101,No. 4 Tianyang 6th Road, Dongfang Community, Shenzhen - CHINA Post Code: 518105
zheng.cheng@jzt.hk
Tel.: +86 0755-27058033
Phone:+86 188-2345-2455