Introduction
In the world of manufacturing, plastic injection molding stands as one of the most widely used processes for producing high-quality, durable plastic parts. However, achieving perfection in this process is no small feat. Even the smallest defect in an injection mold can lead to significant issues, ranging from compromised structural integrity to aesthetic flaws, which can ultimately impact the entire production cycle and increase costs. As the demand for precision and quality in industries like automotive, medical, and consumer goods continues to grow, the need for defect-free plastic injection molds has never been more critical.
This comprehensive guide delves into the masterful techniques that can be employed to significantly reduce defects in plastic injection molds. Whether you are a seasoned professional or a novice in the field, this article aims to equip you with the knowledge and strategies necessary to produce superior-quality plastic parts consistently.
The purpose of this article is to explore the various causes of defects, discuss the design and manufacturing best practices, and introduce advanced troubleshooting and quality control techniques. By understanding and applying these methods, you can enhance the efficiency and reliability of your plastic parts production, ultimately guaranteeing better outcomes and customer satisfaction.
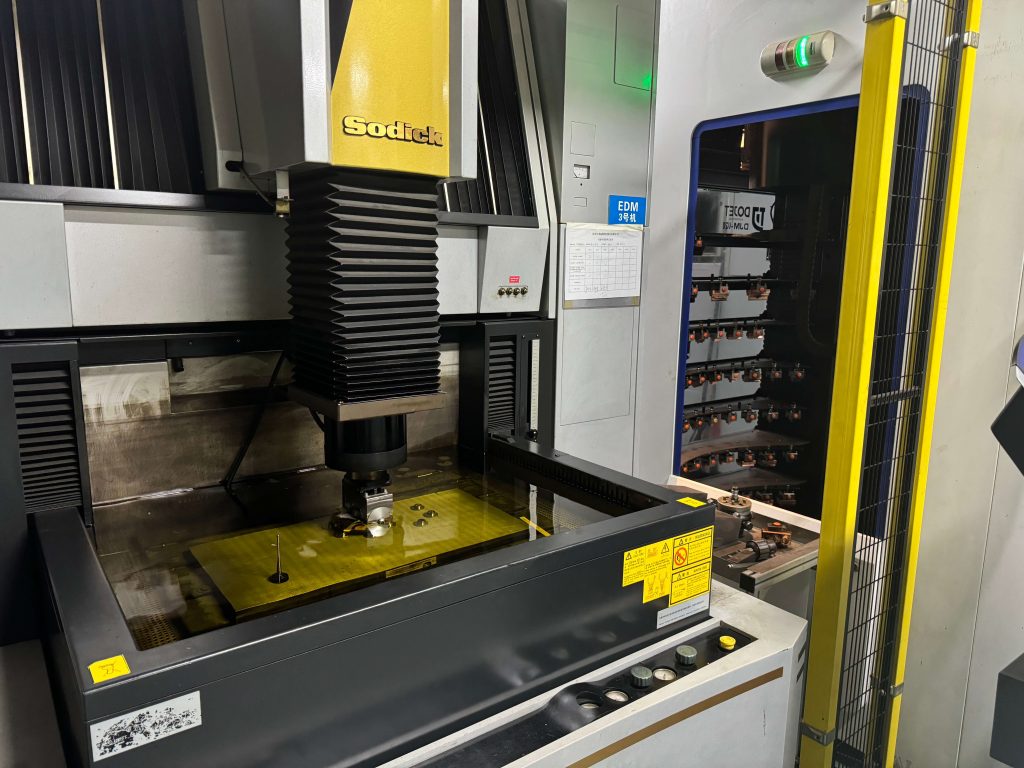
Understanding Common Defects in Plastic Injection Molding
Plastic injection molding, while highly effective, is a complex process with numerous variables that can lead to defects if not properly managed. Understanding these defects, their causes, and how they impact the final product is the first step towards reducing them. Here are some of the most common defects encountered in plastic injection molds:
1. Warping: Warping occurs when different parts of the plastic part cool and solidify at different rates, causing the material to bend or twist. This defect can lead to functional issues and misalignment in assembled parts. Warping is often caused by uneven cooling, improper mold design, or variations in wall thickness.
2. Sink Marks: Sink marks are depressions or indentations that form on the surface of a molded part, usually above thicker sections of the material. These marks are caused by the material shrinking as it cools and can be exacerbated by inadequate packing pressure or cooling time.
3. Burn Marks: Burn marks appear as black or dark brown discolorations on the surface of the molded part. They are usually caused by trapped air or resin degradation due to excessive heating. Burn marks not only affect the appearance but can also weaken the part structurally.
4. Weld Lines: Weld lines occur where two flow fronts meet during the injection process. They appear as visible lines or cracks and can significantly reduce the strength of the part. Weld lines are often caused by improper mold temperature, injection speed, or poor gate design.
5. Short Shots: A short shot is when the mold cavity is not completely filled, resulting in an incomplete part. This defect is usually due to insufficient material, low injection pressure, or improper venting.
6. Flash: Flash is excess material that leaks out of the mold cavity and solidifies on the part’s surface. It is typically caused by improper clamping force, worn-out mold components, or incorrect mold alignment.
7. Voids: Voids are small, empty spaces within the molded part, often caused by trapped air or improper packing. They can reduce the part’s strength and cause cosmetic defects.
8. Bubbles: Bubbles or gas pockets can form within the molded part, usually due to moisture in the material, incorrect temperature settings, or rapid cooling. These bubbles can weaken the part and cause surface imperfections.
Each of these defects can have multiple root causes, making it essential to approach defect reduction with a comprehensive strategy that addresses every aspect of the injection molding process, from design and material selection to manufacturing practices and quality control.
Understanding these defects is not just about identifying them but also about knowing the specific conditions that lead to their occurrence. With this knowledge, it becomes possible to implement targeted measures to prevent defects before they occur, leading to more consistent quality and fewer production delays.
Would you like to proceed with the next section on “Design Considerations to Minimize Defects”?
Design Considerations to Minimize Defects
Designing a plastic injection mold requires meticulous attention to detail. A well-designed mold can significantly reduce the likelihood of defects, while a poorly designed one can lead to costly rework and production delays. Below are key design considerations that, when implemented correctly, can help minimize defects and improve the quality of plastic parts production.
1. Optimal Mold Design:
One of the most critical aspects of defect reduction is optimal mold design. A robust design ensures that the plastic flows evenly and solidifies uniformly, reducing the chances of defects such as warping, sink marks, and short shots. Here are some key elements of optimal mold design:
- Uniform Wall Thickness: Maintaining a consistent wall thickness throughout the part is crucial. Variations in thickness can cause uneven cooling, leading to warping and sink marks. Ideally, the wall thickness should be as uniform as possible to ensure even material flow and cooling.
- Proper Draft Angles: Draft angles are essential for the easy ejection of the part from the mold. A draft angle of 1 to 2 degrees is recommended for most materials. Insufficient draft can cause surface defects and increase the risk of damaging the part during ejection.
- Rib and Boss Design: Ribs and bosses should be designed with care to avoid sink marks and warping. Ribs should be no more than 60% of the wall thickness and should taper slightly to facilitate material flow and cooling. Bosses should be designed with adequate support and minimal wall thickness to prevent voids and sink marks.
- Fillets and Radii: Sharp corners should be avoided in mold design as they can cause stress concentrations and lead to cracking or warping. Instead, use fillets and radii to create smooth transitions between surfaces, which helps in reducing stress and improving material flow.
- Gate Location and Design: The gate is where the molten plastic enters the mold cavity. The location and design of the gate are crucial as they influence how the material flows through the mold. Gates should be placed in a way that allows for even filling and minimizes weld lines and air traps. Common gate types include edge gates, pinpoint gates, and submarine gates, each suited for different part geometries and materials.
2. Material Selection:
Choosing the right material for a specific application is another vital factor in reducing defects. The properties of the plastic material, such as viscosity, shrinkage rate, and thermal stability, can significantly impact the quality of the molded part. Here’s how to make an informed material selection:
- Viscosity: Materials with low viscosity flow more easily and are less likely to cause short shots or flow marks. High-viscosity materials, on the other hand, may require higher injection pressures and are more prone to defects like sink marks and voids.
- Shrinkage: Different materials shrink at different rates as they cool. Choosing a material with predictable and minimal shrinkage can help in maintaining dimensional accuracy and reducing warping.
- Thermal Stability: Materials that can withstand high temperatures without degrading are ideal for processes involving complex mold designs or high injection pressures. This stability helps in preventing burn marks and material degradation.
- Compatibility with Mold Design: The chosen material should be compatible with the mold design in terms of flow characteristics and solidification behavior. For example, high-impact polystyrene (HIPS) is suitable for thin-walled parts, while acrylonitrile butadiene styrene (ABS) works well for parts requiring high impact resistance.
3. Gate Location and Type:
The gate is the point where the molten plastic enters the mold cavity, and its location and type play a crucial role in minimizing defects. Proper gate design ensures even filling of the mold cavity, reduces the risk of air traps, and prevents issues like weld lines and sink marks. Here are some considerations:
- Gate Placement: Place gates in areas that ensure even filling and minimize flow length. Avoid placing gates near thin sections or areas prone to cosmetic defects.
- Gate Size: The gate should be large enough to allow for adequate material flow but small enough to ensure quick solidification once the cavity is filled. This balance helps in reducing short shots and flash.
- Gate Types: Different gate types, such as edge gates, fan gates, and pinpoint gates, are suited for different applications. Choosing the right gate type based on the part design and material properties is essential for minimizing defects.
- Vent Placement: Proper venting is crucial to allow trapped air to escape from the mold cavity. Vents should be placed in areas where air is likely to be trapped, such as the farthest point from the gate or at the corners of the mold cavity.
By integrating these design considerations into the mold development process, manufacturers can significantly reduce the risk of defects and ensure the production of high-quality plastic parts. Design is the foundation of defect-free molding, and careful planning and attention to detail at this stage can save considerable time and resources in the long run.
Manufacturing Best Practices
Even with a well-designed mold, the manufacturing process itself plays a crucial role in determining the quality of the final product. Implementing best practices in the manufacturing process can significantly reduce the likelihood of defects and improve overall production efficiency. Below are some key manufacturing best practices to follow:
1. Tooling Precision and Maintenance:
Precision in mold tooling is fundamental to reducing defects. A precisely machined mold ensures accurate dimensions and surface finishes, which are critical for the quality of the final part. Here’s how to maintain tooling precision:
- High-Precision Machining: Utilize high-precision machining equipment, such as CNC machines, to achieve tight tolerances in mold making. This precision reduces the chances of dimensional inaccuracies and surface defects.
- Regular Mold Maintenance: Regular maintenance of the mold is essential to prevent wear and tear that can lead to defects like flash and mismatched parts. Maintenance activities should include cleaning, lubrication, and inspection for any signs of wear or damage.
- Mold Re-qualification: After a certain number of cycles, molds should be re-qualified to ensure they still meet the required specifications. Re-qualification involves checking dimensions, surface finishes, and critical features to ensure the mold can continue producing defect-free parts.
- Proper Storage: Store molds in a clean, dry environment when not in use. Proper storage prevents rusting and damage, which can lead to defects in subsequent production runs.
2. Temperature Control:
Temperature control is a critical factor in the injection molding process, as it affects the flow and cooling of the molten plastic. Proper temperature management can help reduce defects like warping, sink marks, and burn marks. Here are some tips for effective temperature control:
- Mold Temperature: Maintain a consistent mold temperature to ensure uniform cooling. Uneven mold temperatures can lead to warping and internal stresses in the part. Mold temperature control units (TCUs) can be used to maintain the desired temperature throughout the molding cycle.
- Melt Temperature: The temperature of the molten plastic should be within the recommended range for the specific material being used. Too high a melt temperature can cause burn marks and material degradation, while too low a temperature can lead to short shots and poor surface finish.
- Cooling System Design: Design the cooling system in the mold to provide uniform cooling throughout the part. Use baffles, bubblers, and other cooling components to ensure even heat distribution and prevent hot spots.
- Cycle Time Optimization: Optimize the cycle time to balance quality and efficiency. A longer cooling time can improve part quality by reducing internal stresses and warping, but it can also reduce production efficiency.
3. Pressure Management:
Pressure plays a vital role in the injection molding process. Both injection and holding pressures need to be carefully controlled to ensure that the mold is filled correctly and the part solidifies uniformly. Improper pressure management can lead to defects such as short shots, flash, and sink marks. Here’s how to manage pressure effectively:
- Injection Pressure: The initial injection pressure should be high enough to fill the mold cavity completely but not so high that it causes flash or excessive stress in the part. Monitor and adjust the injection pressure based on part geometry and material properties.
- Holding Pressure: After the mold cavity is filled, holding pressure is applied to pack the material and compensate for shrinkage as it cools. Insufficient holding pressure can cause voids and sink marks, while excessive pressure can lead to flash and internal stresses.
- Pressure Profiles: Use a multi-stage pressure profile during the injection cycle to optimize material flow and packing. For example, a high initial pressure can be used to fill the cavity quickly, followed by a lower pressure to pack the material and minimize internal stresses.
- Vent and Gate Pressure Management: Ensure proper venting to prevent trapped air, which can cause burn marks and incomplete filling. Gate size and location should also be optimized to manage pressure distribution throughout the mold cavity.
Implementing these manufacturing best practices can help maintain consistency and quality in the injection molding process. By focusing on precision, temperature control, and pressure management, manufacturers can significantly reduce the incidence of defects and ensure that their plastic parts meet the required specifications.
Process Optimization Techniques
Process optimization is an ongoing effort to fine-tune the injection molding process to achieve the highest quality and efficiency. By continually monitoring and adjusting process parameters, manufacturers can minimize defects and improve the overall performance of their production lines. Here are some key process optimization techniques:
1. Cycle Time Optimization:
Cycle time is the total time it takes to complete one production cycle, including injection, cooling, and ejection. Optimizing cycle time is crucial for balancing quality and production efficiency. Here’s how to do it:
- Minimize Cooling Time: Cooling time is often the longest part of the cycle. While it’s essential for part quality, reducing it without compromising quality can significantly increase production efficiency. Use mold cooling channels, heat exchangers, and temperature control units to optimize cooling.
- Optimize Injection Speed: Adjust the injection speed to achieve the best balance between fill time and material flow. Too fast an injection speed can cause defects like flash and flow marks, while too slow a speed can lead to short shots.
- Ejection Optimization: Ejection time can be reduced by ensuring proper mold release and using ejector pins and air ejectors effectively. A smooth ejection process reduces cycle time and prevents part damage.
- Parallel Processes: Where possible, perform secondary operations such as insert molding, over-molding, or assembly in parallel with the molding process to optimize overall production time.
2. Injection Speed and Pressure Control:
Injection speed and pressure are critical parameters that need to be carefully controlled to achieve consistent part quality. Variations in these parameters can lead to defects like flash, warping, and burn marks. Here’s how to control them effectively:
- Injection Speed Control: Start with a moderate injection speed and gradually increase it until the cavity fills completely without any defects. Use a multi-stage injection profile to optimize flow and reduce stress in the part.
- Pressure Control: Monitor and adjust injection pressure based on the material’s behavior during the molding cycle. Too high pressure can cause flash and stress, while too low pressure can lead to short shots and poor surface finish.
- Velocity Control: Velocity control is essential for achieving uniform material flow and preventing defects like flow marks and air traps. Use a consistent velocity profile throughout the injection process.
- Back Pressure Optimization: Back pressure during the plasticizing phase should be optimized to ensure uniform material melting and prevent air entrapment. Proper back pressure management also contributes to consistent shot size and material homogeneity.
3. Use of Advanced Sensors and Monitoring Systems:
Advanced sensors and monitoring systems can provide real-time data on various aspects of the injection molding process. This data can be used to identify issues early, make adjustments, and ensure consistent quality. Here’s how to leverage these technologies:
- In-Mold Sensors: Use sensors to monitor temperature, pressure, and flow within the mold cavity. These sensors can provide valuable data on how the material is behaving during the molding process and help identify potential issues.
- Real-Time Monitoring Systems: Implement real-time monitoring systems to track key process parameters such as injection pressure, melt temperature, and cycle time. These systems can alert operators to any deviations from the optimal process window.
- Data Analysis and Process Optimization: Use data from monitoring systems to identify trends and correlations between process parameters and part quality. This data can be used to make informed decisions about process adjustments and optimization.
- Predictive Maintenance: Advanced monitoring systems can also be used for predictive maintenance, identifying potential issues with molds or machinery before they lead to defects or downtime. This proactive approach can significantly improve production efficiency and quality.
By employing these process optimization techniques, manufacturers can achieve a higher level of control over the injection molding process. This control translates into more consistent part quality, fewer defects, and improved overall efficiency.
Advanced Troubleshooting Techniques
Even with the best design and manufacturing practices, defects can still occur. Advanced troubleshooting techniques are essential for identifying the root causes of defects and implementing corrective actions to prevent their recurrence. Here are some advanced troubleshooting techniques that can be applied in plastic injection molding:
1. Root Cause Analysis:
Root cause analysis (RCA) is a systematic approach to identifying the underlying causes of defects. By understanding the root cause, manufacturers can implement effective corrective actions that address the problem at its source. Here’s how to conduct an RCA:
- Define the Problem: Clearly define the defect and its impact on the product. Use quantitative data, such as the percentage of parts affected or the severity of the defect, to quantify the problem.
- Collect Data: Gather data on all relevant process parameters, such as temperature, pressure, cycle time, and material properties. Use tools like process monitoring systems and historical production records to collect accurate data.
- Identify Potential Causes: Use tools like fishbone diagrams, Pareto charts, and 5 Whys analysis to identify potential causes of the defect. Consider all aspects of the process, including design, material, equipment, and environmental factors.
- Test Hypotheses: Test each potential cause by adjusting process parameters and observing the effect on the defect. Use controlled experiments to validate or eliminate potential causes.
- Implement Corrective Actions: Once the root cause has been identified, implement corrective actions to address the problem. Monitor the results to ensure that the corrective actions are effective and that the defect does not recur.
2. Corrective Actions for Specific Defects:
Different defects require different corrective actions. Here’s how to address some of the most common defects in plastic injection molding:
- Sink Marks: Increase holding pressure and time to ensure that the cavity is fully packed. Adjust the cooling system to provide more uniform cooling, and consider redesigning the part to reduce wall thickness variations.
- Weld Lines: Increase mold and melt temperature to improve material flow and reduce weld line formation. Adjust the gate location and injection speed to promote better material bonding at the weld line.
- Short Shots: Increase injection pressure and speed to ensure that the cavity fills completely. Check for obstructions in the runner system and optimize venting to reduce air traps.
- Flash: Reduce injection pressure and check for proper mold clamping force. Inspect the mold for wear or damage and ensure that the parting line is properly aligned.
- Voids and Bubbles: Increase holding pressure and time to pack the material and eliminate voids. Reduce melt temperature and ensure that the material is properly dried to remove moisture.
3. Documenting and Learning from Past Issues:
Documenting defects and the corrective actions taken is essential for continuous improvement. A well-maintained defect log can provide valuable insights into recurring issues and help in developing preventive measures. Here’s how to document and learn from past issues:
- Defect Log: Create a log that records details of each defect, including the type of defect, affected parts, process parameters at the time of occurrence, and the corrective actions taken.
- Root Cause Analysis Documentation: Document the RCA process for each defect, including the potential causes considered, the tests conducted, and the conclusions reached.
- Preventive Measures: Use the data from the defect log and RCA documentation to develop preventive measures that can be implemented in future production runs. This could include changes to mold design, material selection, or process parameters.
- Training and Knowledge Sharing: Share the learnings from defect analysis and corrective actions with the production team. Conduct training sessions to ensure that everyone is aware of the common causes of defects and the best practices for preventing them.
By applying these advanced troubleshooting techniques, manufacturers can quickly and effectively address defects when they occur. This proactive approach to problem-solving helps in maintaining high-quality standards and reducing production downtime.
Automation and Technology Integration
Incorporating automation and advanced technology into the injection molding process can significantly enhance quality control and reduce defects. Automation not only improves consistency and efficiency but also minimizes the chances of human error. Here’s how automation and technology can be leveraged for defect reduction:
1. Using Robotics and Automation for Consistency:
Robotics and automation play a vital role in modern injection molding facilities. They can handle repetitive tasks with high precision and consistency, reducing the likelihood of defects caused by manual intervention. Here’s how to implement robotics and automation:
- Robotic Part Handling: Use robots for part handling, assembly, and packaging. This reduces the risk of damage and contamination caused by manual handling.
- Automated Insert Placement: For insert molding applications, use automated systems to place inserts accurately and consistently. This ensures proper alignment and bonding between the insert and the plastic material.
- Automated Mold Cleaning: Implement automated mold cleaning systems to remove debris and residues from the mold cavity. Regular cleaning helps maintain mold quality and reduces the risk of defects like flash and surface imperfections.
- Automated Inspection Systems: Use automated inspection systems, such as vision systems and laser scanners, to inspect parts for defects. These systems can detect surface defects, dimensional inaccuracies, and other issues that may not be visible to the naked eye.
2. Industry 4.0 and Smart Manufacturing:
Industry 4.0 technologies, such as the Internet of Things (IoT), artificial intelligence (AI), and machine learning, are revolutionizing the injection molding industry. These technologies enable real-time monitoring, predictive maintenance, and data-driven decision-making. Here’s how to leverage smart manufacturing for defect reduction:
- Real-Time Process Monitoring: Use IoT-enabled sensors to monitor key process parameters, such as temperature, pressure, and humidity, in real-time. This data can be used to detect deviations from the optimal process window and take corrective actions before defects occur.
- Predictive Maintenance: Implement predictive maintenance systems that use AI and machine learning to analyze equipment data and predict potential failures. This proactive approach helps prevent unplanned downtime and reduces the risk of defects caused by equipment issues.
- Data Analytics and Optimization: Use data analytics to identify patterns and correlations between process parameters and part quality. This information can be used to optimize the process and reduce the likelihood of defects.
- Digital Twin Technology: Create a digital twin of the injection molding process to simulate different scenarios and optimize process parameters. Digital twin technology allows manufacturers to test and validate changes before implementing them on the production floor, reducing the risk of defects.
By integrating automation and advanced technology into the injection molding process, manufacturers can achieve higher levels of precision, consistency, and efficiency. This technological advancement is key to maintaining competitive advantage and meeting the ever-increasing quality demands of the market.
Quality Control and Inspection Techniques
Quality control and inspection are critical components of the injection molding process. Effective quality control ensures that defects are detected early and that corrective actions can be taken before defective parts reach the customer. Here are some quality control and inspection techniques that can help in maintaining high standards of quality:
1. Inline Inspection Techniques:
Inline inspection techniques are used to monitor the quality of parts as they are being produced. This allows for real-time detection of defects and immediate corrective actions. Here are some inline inspection methods:
- Vision Systems: Vision systems use cameras and image processing software to inspect parts for surface defects, dimensional accuracy, and other quality criteria. They can be integrated into the production line to inspect every part produced.
- Laser Scanning: Laser scanners can be used to measure the dimensions and surface profiles of parts with high precision. This data can be compared to the CAD model to detect deviations and ensure that parts meet the required specifications.
- Thermal Imaging: Thermal imaging cameras can be used to monitor the temperature distribution of parts as they cool. This helps in detecting defects like warping and internal stresses caused by uneven cooling.
- Weight Monitoring: Weighing each part as it is produced can help detect short shots and material inconsistencies. Automated weighing systems can be integrated into the production line for continuous monitoring.
2. Post-Production Quality Control:
Post-production quality control involves inspecting parts after they have been molded and ejected from the mold. This is the final opportunity to detect and address defects before the parts are shipped to the customer. Here are some post-production inspection techniques:
- Visual Inspection: Manual visual inspection is a simple but effective method for detecting surface defects, such as scratches, flash, and color variations. Trained inspectors can quickly identify and reject defective parts.
- Dimensional Inspection: Dimensional inspection involves measuring critical dimensions of the part using tools like calipers, micrometers, and coordinate measuring machines (CMMs). This ensures that the part meets the required tolerances.
- Functional Testing: For parts that must meet specific functional requirements, such as snap fits or sealing features, functional testing can be performed to ensure that the parts perform as expected.
- Sample Testing: In cases where 100% inspection is not feasible, sample testing can be performed. A statistically significant sample of parts is tested, and the results are used to infer the quality of the entire batch.
3. Statistical Process Control (SPC):
Statistical Process Control (SPC) is a data-driven approach to monitoring and controlling the injection molding process. SPC uses statistical methods to detect variations in the process and identify potential quality issues before they result in defects. Here’s how to implement SPC:
- Control Charts: Use control charts to monitor key process parameters, such as temperature, pressure, and cycle time. Control charts can help detect trends and shifts in the process that may lead to defects.
- Process Capability Analysis: Conduct process capability analysis to determine the ability of the process to produce parts within the specified tolerances. The Cp and Cpk indices are commonly used to assess process capability.
- Pareto Analysis: Use Pareto analysis to identify the most common defects and their causes. This helps prioritize corrective actions and focus on the issues that have the greatest impact on quality.
- Root Cause Analysis: When defects are detected, use root cause analysis to identify the underlying causes and implement corrective actions. This prevents the recurrence of the same defects in future production runs.
By implementing these quality control and inspection techniques, manufacturers can ensure that defects are detected and addressed at the earliest possible stage. This proactive approach to quality control helps in maintaining high standards of quality and reducing the risk of customer complaints and returns.
Case Studies and Real-World Applications
Case studies provide valuable insights into how companies have successfully reduced defects in plastic injection molding through the implementation of best practices and advanced technologies. These real-world examples highlight the challenges faced and the solutions implemented to achieve defect-free production. Here are two case studies from different industries:
1. Case Study 1: Automotive Industry Application
Background: A leading automotive parts manufacturer was experiencing a high rejection rate due to warping and weld lines in their molded parts. These defects were affecting the fit and finish of the parts, leading to assembly issues and customer complaints.
Challenges: The main challenges were maintaining dimensional stability and minimizing weld lines in complex geometries with varying wall thicknesses. The parts required high precision to meet the stringent quality standards of the automotive industry.
Solution: The company implemented several measures to address these issues:
- Mold Flow Analysis: The manufacturer used mold flow simulation software to analyze the material flow and identify potential problem areas in the mold design. Based on the analysis, they optimized the gate location and modified the cooling system to ensure even cooling throughout the part.
- Material Selection: The company switched to a high-flow, low-shrinkage material that provided better dimensional stability and reduced the occurrence of warping.
- Process Optimization: They optimized the injection speed and pressure profiles to achieve a more uniform material flow and reduce the formation of weld lines. The cycle time was also adjusted to ensure adequate cooling before ejection.
- Advanced Quality Control: The manufacturer implemented inline inspection using vision systems to detect weld lines and warping immediately after molding. Defective parts were rejected before reaching the assembly line.
Results: The rejection rate due to warping and weld lines was reduced by over 70%. The improvements in part quality led to fewer assembly issues and a significant reduction in customer complaints.
2. Case Study 2: Medical Device Molding
Background: A medical device manufacturer was facing challenges in producing defect-free parts for a critical component of a medical device. The parts required high precision and surface finish to meet regulatory standards.
Challenges: The main challenges were achieving tight dimensional tolerances and avoiding surface defects like flow marks and blemishes. The parts were made from a high-performance polymer that was prone to defects during molding.
Solution: The company took the following steps to address the challenges:
- Tooling Precision: The mold was re-machined to tighter tolerances to ensure precise dimensions and smooth surface finishes. Electro-polishing was used to achieve a mirror-like surface finish in the mold cavity.
- Temperature and Pressure Control: The manufacturer implemented advanced temperature and pressure control systems to maintain consistent process parameters. A closed-loop control system was used to monitor and adjust the mold temperature and injection pressure in real-time.
- Material Conditioning: The material was dried and pre-conditioned to remove any moisture that could cause defects like bubbles and voids. The material was also tested for consistency before molding.
- Post-Molding Inspection: A comprehensive post-molding inspection process was implemented, including dimensional inspection, visual inspection, and functional testing. Any defects were documented and analyzed for root cause.
Results: The manufacturer achieved a defect rate of less than 0.5%, meeting the stringent quality standards required for medical devices. The improved process control and quality assurance practices led to increased customer satisfaction and compliance with regulatory requirements.
Lessons Learned: These case studies highlight the importance of a holistic approach to defect reduction, encompassing design optimization, process control, and quality assurance. By understanding the specific challenges of each application and implementing targeted solutions, manufacturers can achieve defect-free production and meet the high-quality standards of demanding industries.
Conclusion
Reducing defects in plastic injection molding is a complex but achievable goal that requires a comprehensive approach. From thoughtful mold design and material selection to precise manufacturing practices and advanced process optimization, every step plays a crucial role in minimizing defects and ensuring high-quality plastic parts production.
By understanding common defects and their causes, manufacturers can take proactive measures to prevent them. Implementing best practices in mold design, temperature control, and pressure management can significantly reduce the likelihood of defects. Advanced troubleshooting techniques and the use of automation and technology can further enhance quality control and ensure consistent production outcomes.
Quality control and inspection are critical to detecting and addressing defects early in the process. By employing techniques like inline inspection, statistical process control, and root cause analysis, manufacturers can maintain high standards of quality and minimize the risk of defects reaching the customer.
The case studies presented demonstrate that achieving defect-free production is possible, even in the most demanding industries. By adopting a proactive and systematic approach to defect reduction, manufacturers can improve product quality, reduce costs, and enhance customer satisfaction.
As the injection molding industry continues to evolve, embracing new technologies and best practices will be essential to maintaining a competitive edge. With a commitment to quality and continuous improvement, manufacturers can ensure the production of high-quality, defect-free plastic parts for years to come.
Additional Resources
To further enhance your knowledge and skills in plastic injection molding, consider exploring the following resources:
- Books:
- “Injection Molding Handbook” by Dominick V. Rosato
- “Troubleshooting Injection Molding” by Vannessa Goodship
- “Plastics Engineering” by R.J. Crawford
- Online Courses:
- Injection Molding Process Control by the University of Wisconsin-Madison
- Plastic Injection Molding 101 by Udemy
- Advanced Injection Molding by Plastics Technology
- Industry Associations:
- Society of Plastics Engineers (SPE)
- Plastics Industry Association (PLASTICS)
- European Plastics Converters (EuPC)
These resources provide valuable insights and practical knowledge that can help you stay updated on the latest trends and best practices in plastic injection molding.
With these techniques and resources, you are now equipped to tackle the challenges of defect reduction in plastic injection molding and achieve superior quality in your plastic parts production.