Why Choosing the Right Molding Partner is Crucial
When it comes to the automotive industry, the importance of high-quality plastic parts cannot be overstated. Whether it’s the components under the hood, the interior fixtures, or the exterior body parts, each piece plays a critical role in the vehicle’s overall performance, safety, and longevity. Choosing the right automotive plastic injection molding company is not just a decision—it’s a pivotal step that impacts the entire production process, from design and development to manufacturing and quality assurance.
The complexity of automotive plastic parts demands precision, consistency, and a deep understanding of the industry’s standards and regulations. A subpar mold or poorly manufactured part can lead to significant issues down the line, including product recalls, safety hazards, and damage to your brand’s reputation. Therefore, selecting a reliable plastic parts manufacturer is vital to ensuring that your products meet the highest quality standards while remaining cost-effective and efficient.
In this comprehensive guide, we will delve into every aspect of choosing the right automotive plastic injection molding company. From defining your project requirements to evaluating potential partners based on their technical capabilities, quality control measures, and customer service, this article will equip you with the knowledge you need to make an informed decision.
By the end of this guide, you will not only understand what to look for in a plastic parts molding company but also how to assess whether a potential partner aligns with your specific needs and expectations. Let’s begin by understanding your needs in the context of automotive injection molding.
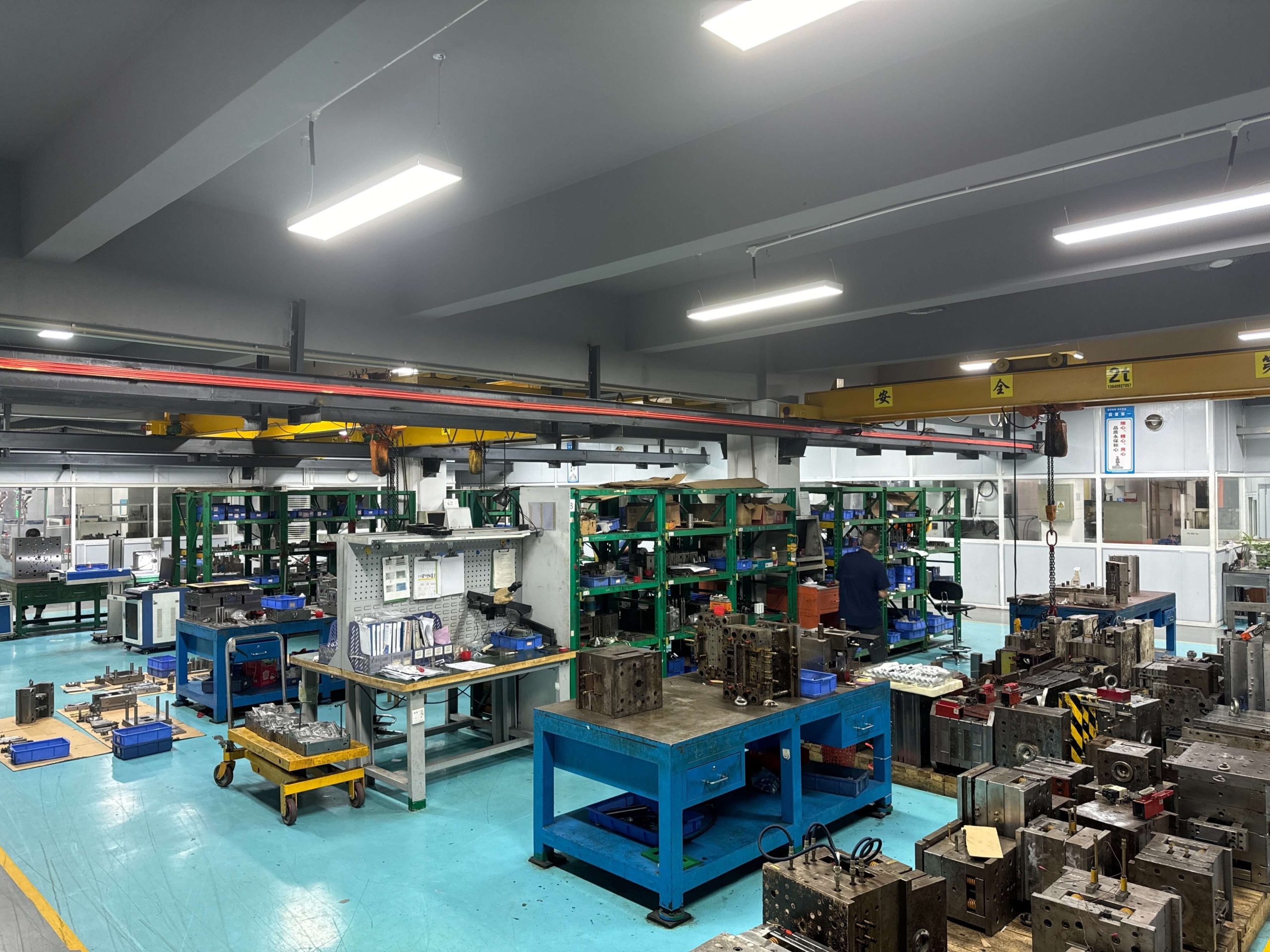
Understanding Your Needs
Define Your Project Requirements
Before you can effectively evaluate potential plastic parts manufacturers, it is essential to have a clear understanding of your own project requirements. This involves identifying the specific type of plastic parts you need, as well as any unique challenges that your project may present.
First, consider the application of the plastic parts in the automotive industry. Are they intended for interior components such as dashboards, door panels, and air vents? Or are they critical exterior elements like bumpers, grilles, and mirror housings? Perhaps they are under-the-hood parts, such as engine covers, coolant reservoirs, or air intake manifolds, which require a higher degree of thermal and chemical resistance.
Each of these applications comes with its own set of requirements. For example, interior components might prioritize aesthetics, durability, and UV resistance, while under-the-hood parts would demand high thermal stability, mechanical strength, and resistance to automotive fluids. Understanding these requirements upfront will help you determine the types of materials needed, as well as the specific molding processes that should be employed.
Additionally, consider the complexity of the parts you need. Are they simple components with a straightforward design, or do they have intricate geometries that require advanced molding techniques like overmolding or insert molding? Complex designs often necessitate more sophisticated tooling and expertise, which not all manufacturers may possess.
Another critical factor is the volume of production. Are you looking to produce a small batch of custom parts, or do you require mass production of millions of units? The production volume will influence the type of mold required, the machinery used, and the overall cost of the project. High-volume production typically requires more robust and durable molds, often made from hardened steel, to withstand the wear and tear of repeated use.
Finally, you should have a clear timeline for your project. Consider any deadlines for product launch, regulatory approvals, or production schedules. A realistic timeline will help you assess whether a potential plastic parts manufacturer has the capacity and flexibility to meet your deadlines without compromising quality.
Budget Considerations
Once you have defined your project requirements, the next step is to establish a budget that balances cost with quality. While it may be tempting to choose the lowest-cost option, it is crucial to remember that in the automotive industry, the consequences of poor-quality parts can be severe. Investing in a reputable and experienced plastic parts molding company may involve higher upfront costs, but it can save you from costly recalls, warranty claims, and damage to your brand’s reputation in the long run.
When setting your budget, consider not just the cost of the molds and the per-unit price of the parts, but also any hidden costs that may arise. For instance, mold maintenance is an often-overlooked expense that can add up over time. Regular maintenance is essential to ensure the longevity of the mold and the consistency of the parts produced. Failure to maintain molds properly can result in defects, production delays, and increased scrap rates.
Shipping costs are another factor to consider, especially if you are working with a manufacturer located in a different country. International shipping can be expensive, particularly for large and heavy molds. Additionally, the time it takes for parts to be shipped to your production facility can impact your overall timeline and costs.
It is also worth considering the total cost of ownership (TCO) when evaluating potential manufacturers. TCO includes not only the initial costs of molds and parts but also ongoing expenses such as maintenance, repairs, and energy consumption during production. A manufacturer that offers energy-efficient processes and durable molds may provide a lower TCO in the long run, even if their initial quote is higher.
Negotiation is an essential part of the budgeting process. Don’t hesitate to discuss payment terms, volume discounts, and potential cost-saving measures with your prospective molding partners. For instance, committing to a long-term partnership or agreeing to a minimum order quantity may result in more favorable pricing.
In conclusion, understanding your project requirements and budget constraints is the first step in selecting the right automotive plastic injection molding company. With this foundation in place, you can begin to evaluate potential partners based on the key factors that will determine their suitability for your specific needs.
As we move forward, we will explore these factors in detail, starting with the importance of experience and expertise in the automotive injection molding industry.
Key Factors to Consider When Choosing a Molding Company
Experience and Expertise
When selecting an automotive plastic injection molding company, experience and expertise are among the most critical factors to consider. The automotive industry has stringent standards and regulations that must be adhered to, and only a manufacturer with a deep understanding of these requirements can consistently deliver parts that meet or exceed expectations.
Industry-Specific Experience
Experience in the automotive industry is not just about the number of years a company has been in business. It’s about their track record of successfully handling projects similar to yours. Automotive parts require precise engineering, rigorous testing, and a thorough understanding of how these components interact with other parts of the vehicle. Therefore, the best plastic parts manufacturers are those who have extensive experience specifically in the automotive sector.
Look for a company that can provide case studies or examples of previous automotive projects. These case studies should demonstrate their ability to produce high-quality parts that meet industry standards, as well as their capability to handle the complexities of automotive projects, such as working with various materials, meeting tight tolerances, and adhering to stringent quality control processes.
For instance, a company with a portfolio that includes the production of engine components, interior parts, and exterior body elements is likely to have a comprehensive understanding of the diverse needs of the automotive industry. This experience ensures that they are well-equipped to tackle the unique challenges your project may present.
Technical Expertise
Technical expertise is another crucial aspect. A competent automotive injection molding company should possess advanced technical knowledge and capabilities that enable them to manage complex projects efficiently. This includes expertise in mold design, material selection, and the various molding processes that may be required for your specific parts.
For example, if your project involves parts with complex geometries or the use of multiple materials, the manufacturer should have experience with advanced molding techniques such as overmolding, insert molding, or two-shot molding. These processes require precise control over the injection molding parameters and a deep understanding of the behavior of different materials during the molding process.
Additionally, the company should have in-depth knowledge of the various types of plastics used in the automotive industry, such as ABS, polycarbonate, polypropylene, and nylon. Each material has its own set of properties that make it suitable for different applications. A knowledgeable manufacturer will be able to advise you on the best material for your specific part, taking into account factors like strength, flexibility, thermal resistance, and cost.
Technical Capabilities
The technical capabilities of a plastic parts manufacturer are directly related to the quality and efficiency of the production process. Advanced machinery, state-of-the-art technology, and a well-equipped facility are all indicators of a company’s ability to produce high-quality automotive parts at scale.
Range of Services
A comprehensive range of services is a strong indicator that a company has the technical capabilities needed to handle your project from start to finish. This includes not only injection molding but also related services such as design and engineering, prototyping, tooling, and post-production finishing.
For instance, a manufacturer that offers in-house design and engineering support can assist you in optimizing your part design for manufacturability. This collaboration during the design phase can help identify potential issues early on, such as difficult-to-mold features or material incompatibilities, saving time and money in the long run.
Prototyping services are also crucial, especially if your project involves new or innovative parts. Rapid prototyping allows you to test and refine your design before committing to full-scale production. A manufacturer with the capability to produce high-quality prototypes can help you validate your design, identify potential improvements, and ensure that the final product meets your requirements.
Advanced Machinery and Technology
The quality of the machinery and technology used in the production process is another critical factor. In the automotive industry, where precision and consistency are paramount, the use of advanced equipment is essential.
Look for a company that utilizes state-of-the-art machinery, such as high-precision CNC machines, automated injection molding machines, and advanced quality control equipment like coordinate measuring machines (CMM). These tools enable the manufacturer to produce parts with tight tolerances and consistent quality, even in large production runs.
For example, automated injection molding machines equipped with robotic arms can improve production efficiency and reduce the risk of human error. These machines can handle complex parts with intricate details, ensuring that each piece meets the exact specifications.
In addition to machinery, consider the company’s technological capabilities in terms of software and digital tools. Advanced CAD/CAM software, for instance, allows for precise mold design and simulation, helping to predict potential issues before production begins. Similarly, digital twin technology and other Industry 4.0 tools can provide real-time monitoring and optimization of the production process, leading to higher efficiency and reduced waste.
Quality Control Measures
Quality control is one of the most important aspects of plastic parts manufacturing, particularly in the automotive industry. A robust quality control system ensures that every part produced meets the required standards, reducing the risk of defects and ensuring the safety and reliability of the final product.
Certifications to Look For
When evaluating a plastic parts molding company, check for industry certifications that demonstrate their commitment to quality. Certifications such as ISO 9001, IATF 16949, and ISO 14001 are indicators of a company’s adherence to international standards for quality management, automotive industry requirements, and environmental management, respectively.
ISO 9001 is a widely recognized quality management standard that ensures a company has the processes in place to consistently produce high-quality products. IATF 16949, on the other hand, is specific to the automotive industry and covers additional requirements related to defect prevention, continuous improvement, and the reduction of variation and waste in the supply chain.
ISO 14001 certification demonstrates a company’s commitment to environmental management, ensuring that their processes minimize environmental impact. This is particularly important in the automotive industry, where sustainability and environmental responsibility are becoming increasingly critical.
In-House Quality Control Processes
In addition to certifications, inquire about the manufacturer’s in-house quality control processes. A comprehensive quality control system should include rigorous testing at various stages of the production process, from the inspection of raw materials to the final inspection of finished parts.
For example, many leading automotive plastic parts manufacturers use coordinate measuring machines (CMM) to verify the dimensional accuracy of parts. CMMs provide precise measurements that can detect even the smallest deviations from the specified tolerances, ensuring that each part meets the required standards.
Other common quality control measures include non-destructive testing (NDT) methods such as ultrasonic testing, X-ray inspection, and dye penetrant inspection. These techniques allow for the detection of internal defects, such as voids, cracks, or inclusions, without damaging the part.
Furthermore, ask about the company’s approach to process control. Do they use statistical process control (SPC) techniques to monitor and control production parameters? SPC helps identify trends and variations in the production process, allowing for corrective actions to be taken before defects occur.
Finally, consider the company’s approach to continuous improvement. A manufacturer that is committed to quality will have processes in place for identifying and implementing improvements, whether through lean manufacturing principles, Six Sigma methodologies, or other continuous improvement initiatives.
Design and Development Support
The design and development phase is critical in the production of automotive plastic parts. Collaborating closely with your molding partner during this stage can result in a more efficient manufacturing process, reduced costs, and a higher-quality final product.
In-House Engineering and Design Assistance
One of the key advantages of working with a full-service plastic parts manufacturer is access to in-house engineering and design expertise. An experienced engineering team can provide valuable input on the design of your parts, helping to optimize them for the injection molding process.
For example, engineers can advise on the appropriate wall thickness for your parts, ensuring that they are strong enough to withstand the demands of their application without being overly heavy or difficult to mold. They can also suggest design modifications that reduce the likelihood of defects such as sink marks, warping, or voids.
In addition to optimizing the design for manufacturability, engineers can assist with material selection, helping you choose the best plastic for your application based on factors like strength, flexibility, thermal resistance, and chemical compatibility.
Collaboration During the Design Phase
Collaboration between your team and the manufacturer during the design phase is essential to ensure that the final product meets your requirements. This collaborative approach allows for the early identification and resolution of potential issues, reducing the risk of costly changes or delays later in the process.
For example, the manufacturer’s engineers may identify design features that could cause issues during molding, such as sharp corners or deep undercuts. By addressing these issues early on, you can avoid problems like incomplete fills or excessive wear on the mold, which can lead to defects or increased maintenance costs.
Moreover, collaboration during the design phase can lead to innovative solutions that improve the functionality or performance of your parts. For instance, the manufacturer may suggest using a multi-material molding process, such as overmolding or insert molding, to create parts with enhanced properties, such as improved strength, flexibility, or resistance to wear and tear.
Customization and Flexibility
In the automotive industry, where every project can have unique requirements, customization and flexibility are key attributes of a good plastic parts manufacturer. The ability to handle custom designs and adapt to changing requirements is essential for meeting the specific needs of your project.
Ability to Handle Custom Designs and Modifications
Whether you require a completely custom part or modifications to an existing design, the manufacturer should be able to accommodate your needs. This capability is particularly important in the automotive industry, where parts may need to be tailored to specific vehicle models or performance requirements.
A manufacturer with experience in custom projects will have the expertise and resources needed to design and produce parts that meet your exact specifications. They should be able to work with a wide range of materials and molding processes, and have the ability to create complex geometries or integrate multiple components into a single part.
Additionally, the manufacturer should be willing and able to make modifications to the design as needed, whether due to changes in your requirements, feedback from testing, or the need to improve manufacturability. This flexibility is crucial for ensuring that the final product meets your expectations.
Flexibility in Production Scaling
Flexibility is also important when it comes to production scaling. The automotive industry often requires manufacturers to ramp up production quickly to meet demand, and a good plastic parts manufacturer should be able to scale their production capacity accordingly.
For example, if your project requires an initial small batch for testing or prototyping, the manufacturer should be able to produce this batch efficiently without incurring excessive costs. Then, if the project moves to full-scale production, they should have the capacity to increase output to meet the higher volume requirements.
This scalability is often facilitated by the use of modular molds, which can be reconfigured to produce different parts or adjusted to increase production capacity. A manufacturer with flexible production capabilities will be better equipped to meet your needs, whether you require a few thousand parts or millions.
In summary, experience, expertise, technical capabilities, and quality control measures are all critical factors to consider when choosing an automotive plastic injection molding company. Additionally, the ability to provide design and development support, as well as the flexibility to handle custom designs and scale production, will ensure that your project runs smoothly from start to finish.
With these factors in mind, you can begin to assess potential manufacturing partners based on their production capabilities, reputation, and overall suitability for your project. Next, we’ll delve into how to evaluate the production capabilities of a plastic parts manufacturer.
Evaluating Production Capabilities
Production Capacity
One of the most important aspects to evaluate when choosing an automotive plastic injection molding company is their production capacity. This refers to the manufacturer’s ability to meet your required production volumes within your specified timeline, without compromising on quality.
Number and Type of Injection Molding Machines
The production capacity of a plastic parts manufacturer is largely determined by the number and type of injection molding machines they have at their disposal. Different types of machines are suited to different types of parts, and a manufacturer with a diverse range of machines is better equipped to handle a variety of projects.
For example, small parts with intricate details may require precision molding machines that can handle tight tolerances and complex geometries. Larger parts, on the other hand, may require high-tonnage machines capable of injecting large volumes of plastic in a single shot. Additionally, multi-cavity molds, which produce multiple parts in each cycle, can significantly increase production efficiency for high-volume projects.
When evaluating a manufacturer’s production capacity, ask about the tonnage range of their injection molding machines. Tonnage refers to the clamping force of the machine, and it is an important factor in determining the types of parts the machine can produce. For example, a 55-ton machine might be suitable for small, lightweight parts, while a 380-ton machine would be needed for larger, more robust components.
It’s also important to consider the level of automation in the manufacturer’s facility. Automated machines equipped with robotic arms can improve production efficiency and consistency, reduce labor costs, and minimize the risk of defects. Additionally, automation allows for faster production cycles and the ability to run machines around the clock, further increasing capacity.
Ability to Handle Large Volume Orders
If your project requires the production of millions of parts, it is essential to choose a manufacturer with the capacity to handle large volume orders. This includes not only having enough machines to meet demand but also having the infrastructure and resources to manage high-volume production efficiently.
For instance, high-volume production often requires multiple shifts of workers, stringent process control, and robust logistics management to ensure that materials are available when needed and that finished parts are shipped out on time. A manufacturer with experience in large-scale production will have established processes in place to manage these challenges, ensuring that your project is completed on schedule.
It’s also worth considering whether the manufacturer has the capacity to handle potential increases in demand. If your product is successful, you may need to ramp up production quickly, and a manufacturer with flexible capacity will be better able to accommodate these changes.
Tooling Capabilities
The quality of the mold, or tool, used in the injection molding process is one of the most important factors in determining the quality of the final parts. Therefore, a manufacturer’s tooling capabilities are a critical consideration when choosing a plastic parts manufacturer.
Expertise in Mold Design and Fabrication
Mold design and fabrication are highly specialized fields that require a deep understanding of both the injection molding process and the specific requirements of the parts being produced. A well-designed mold will ensure that parts are produced consistently and with high precision, while a poorly designed mold can lead to defects, increased scrap rates, and higher production costs.
When evaluating a manufacturer’s tooling capabilities, inquire about their expertise in mold design. Do they have in-house mold designers with experience in the automotive industry? Can they provide examples of previous molds they have designed and produced? A manufacturer with a strong background in mold design will be better equipped to create molds that meet your specific requirements.
It’s also important to consider the manufacturer’s fabrication capabilities. Mold fabrication involves the machining of steel or aluminum blocks to create the cavities that will form the parts. This requires advanced CNC machines and other precision tools, as well as skilled machinists who can work to tight tolerances.
Additionally, ask about the materials used in mold fabrication. High-quality molds are typically made from hardened steel, which is durable and capable of withstanding the high pressures and temperatures involved in the injection molding process. Aluminum molds, while less durable, can be a cost-effective option for low-volume production or prototyping.
Maintenance and Lifecycle of Molds
Mold maintenance is another critical aspect of tooling capabilities. Over time, molds can wear out, leading to defects in the parts produced. Regular maintenance is essential to extend the life of the mold and ensure consistent part quality.
When choosing a plastic parts manufacturer, inquire about their mold maintenance practices. Do they have a dedicated maintenance team? How often are molds inspected and serviced? A manufacturer with a proactive approach to mold maintenance will be able to detect and address issues before they impact production.
It’s also worth considering the expected lifecycle of the mold. A high-quality mold can last for millions of cycles, while a lower-quality mold may need to be replaced after just a few hundred thousand cycles. Understanding the expected lifespan of the mold will help you plan for future production needs and budget for potential replacements.
Lead Time and Turnaround
In the fast-paced automotive industry, lead time and turnaround are critical factors in determining the success of a project. The ability to produce high-quality parts quickly and efficiently can give you a competitive edge, while delays in production can lead to missed deadlines and lost opportunities.
Standard Production Lead Times
When evaluating a plastic parts manufacturer, ask about their standard production lead times. This includes the time it takes to design and fabricate the mold, as well as the time required for the injection molding process itself.
Lead times can vary depending on the complexity of the parts, the type of mold being used, and the manufacturer’s production schedule. For example, a simple part with a straightforward design may have a lead time of just a few weeks, while a complex part with intricate details or multi-material construction may take several months to produce.
In addition to the standard lead time, consider the manufacturer’s ability to meet your specific timeline. If you have a tight deadline, it’s important to choose a manufacturer with the capacity and flexibility to prioritize your project and meet your deadlines without compromising on quality.
Flexibility to Meet Tight Deadlines
In some cases, you may need to expedite production to meet an urgent deadline, such as a product launch or a response to a sudden increase in demand. In these situations, it’s essential to work with a manufacturer that can offer flexible production scheduling and the ability to accelerate lead times.
For example, a manufacturer with a robust production infrastructure may be able to allocate additional resources to your project, such as dedicating extra machines or running additional shifts. They may also have the ability to fast-track the mold design and fabrication process, reducing the overall lead time.
When discussing lead times with potential manufacturers, be sure to ask about their flexibility in meeting tight deadlines. A manufacturer with a track record of delivering projects on time, even under challenging circumstances, will give you confidence that your project will be completed successfully.
Assessing the Company’s Reputation
Customer Reviews and Testimonials
One of the most reliable ways to assess a plastic parts manufacturer’s reputation is by reviewing customer feedback. Testimonials, case studies, and online reviews provide valuable insights into the experiences of other clients and can help you gauge the reliability and quality of the manufacturer’s services.
Importance of Third-Party Reviews and Client Feedback
Third-party reviews are particularly valuable because they are often more impartial than testimonials provided directly by the manufacturer. Platforms like Google Reviews, Clutch, or industry-specific forums can provide honest feedback from clients who have worked with the manufacturer.
When reviewing feedback, pay attention to common themes. Are clients consistently praising the manufacturer for their quality, communication, and on-time delivery? Or are there recurring complaints about issues such as poor customer service, missed deadlines, or inconsistent part quality?
It’s also helpful to look for reviews from clients in the automotive industry. While general reviews can provide useful information, feedback from other automotive clients will be more relevant to your specific needs.
Red Flags to Watch Out For
While positive reviews are a good sign, it’s equally important to watch out for red flags in the feedback. Some potential warning signs include:
- Frequent Complaints About Quality: If multiple clients mention issues with part quality, this could indicate a problem with the manufacturer’s quality control processes.
- Lack of Responsiveness: Complaints about poor communication or unresponsive customer service are also red flags. A reliable manufacturer should be easy to contact and quick to address any issues that arise.
- Missed Deadlines: Consistent reports of missed deadlines can indicate that the manufacturer is overcommitting or lacks the capacity to handle their workload.
If you come across any of these red flags, it’s worth investigating further to determine whether the issues are isolated incidents or part of a broader pattern.
Case Studies and Portfolio
In addition to customer reviews, reviewing the manufacturer’s portfolio and case studies can provide a deeper understanding of their capabilities and experience. A strong portfolio should showcase a variety of projects that demonstrate the manufacturer’s ability to handle complex and diverse automotive injection molding projects.
Reviewing Past Projects Similar to Your Needs
When reviewing the manufacturer’s portfolio, look for projects that are similar to your own. For example, if you need high-precision engine components, look for case studies that highlight the manufacturer’s experience in producing similar parts. If your project involves custom interior components, seek out examples of previous work in that area.
Case studies should provide detailed information about the challenges faced during the project, the solutions implemented by the manufacturer, and the results achieved. This information can give you confidence that the manufacturer has the expertise and problem-solving skills needed to handle your project successfully.
Evidence of Successful Project Completion
A good case study will also provide evidence of successful project completion, such as meeting or exceeding client expectations, delivering parts on time, and achieving high levels of quality. This evidence can include client testimonials, quality certifications, or performance metrics such as defect rates or production efficiency.
If possible, ask the manufacturer for references from past clients. Speaking directly with other clients who have worked with the manufacturer can provide valuable insights and help you make a more informed decision.
Industry Reputation
In addition to customer reviews and case studies, it’s important to consider the manufacturer’s overall reputation within the industry. A strong reputation can be an indicator of a company’s reliability, quality, and commitment to excellence.
Awards, Recognitions, or Affiliations with Industry Bodies
Awards and recognitions from industry organizations are a good sign that the manufacturer is respected by their peers and has a track record of success. These awards can be for quality, innovation, customer service, or other areas of excellence.
Affiliations with industry bodies, such as the Society of Plastics Engineers (SPE) or the Automotive Industry Action Group (AIAG), are also indicators of a manufacturer’s commitment to staying up-to-date with industry trends and best practices. Membership in these organizations often requires adherence to high standards and ongoing professional development.
When evaluating a manufacturer’s industry reputation, consider whether they are recognized as a leader in their field and whether they are actively involved in industry events, conferences, and publications.
Location and Logistics
Geographical Location
The geographical location of the plastic parts manufacturer is an important consideration, particularly if your production facility is located in a different region or country. The distance between the manufacturer and your facility can impact shipping costs, lead times, and the overall logistics of your project.
Proximity to Your Manufacturing Facility
If possible, choosing a manufacturer located near your production facility can provide several advantages. Shorter shipping distances can reduce transportation costs and lead times, making it easier to manage inventory and meet production schedules.
Proximity also allows for easier communication and collaboration. If issues arise during production, it’s often easier to resolve them when the manufacturer is located nearby. Additionally, being able to visit the manufacturer’s facility in person can provide valuable insights into their operations and help build a stronger working relationship.
However, if you are considering working with an international manufacturer, it’s important to weigh the benefits of cost savings or specialized expertise against the potential challenges of long-distance logistics.
Impact on Shipping Costs and Lead Times
Shipping costs can vary significantly depending on the distance between the manufacturer and your production facility, as well as the size and weight of the parts being shipped. For large or heavy parts, shipping costs can be a substantial portion of the total project budget.
In addition to cost, consider the impact of shipping on lead times. International shipping can add several weeks to the overall production timeline, which may be a critical factor if you are working under tight deadlines.
To mitigate these challenges, some manufacturers offer just-in-time (JIT) delivery options, where parts are produced and shipped in smaller batches as needed, rather than in large quantities all at once. This approach can help reduce inventory costs and ensure that parts are available when needed, without the need for long-term storage.
Logistics and Supply Chain Management
Effective logistics and supply chain management are essential for ensuring that parts are delivered on time and in good condition. A manufacturer with strong logistics capabilities will have established processes in place to manage the transportation, storage, and distribution of parts, both domestically and internationally.
Company’s Experience with International Shipping
If you are working with an international manufacturer, it’s important to choose a company with extensive experience in global logistics. This includes knowledge of customs regulations, import/export requirements, and the ability to navigate potential challenges such as delays, tariffs, or transportation disruptions.
An experienced manufacturer will have established relationships with reliable shipping partners and will be able to provide accurate estimates of shipping times and costs. They should also have contingency plans in place to address potential issues, such as rerouting shipments or expediting deliveries if necessary.
Inventory Management and Just-in-Time Delivery Options
Effective inventory management is another critical aspect of logistics. A manufacturer that offers just-in-time (JIT) delivery can help you minimize inventory costs and reduce the risk of stockouts or overstocking.
JIT delivery involves producing and shipping parts in smaller batches, timed to coincide with your production schedule. This approach allows you to keep inventory levels low while ensuring that parts are available when needed, without the need for long-term storage.
When evaluating a manufacturer’s logistics capabilities, ask about their approach to inventory management and their ability to offer JIT delivery. A manufacturer with strong logistics and supply chain management processes will be better equipped to meet your needs and ensure that your project runs smoothly.
Cost Considerations
Upfront Costs vs. Long-Term Value
Cost is a critical factor in any manufacturing project, but it’s important to consider not just the upfront costs, but also the long-term value that a plastic parts manufacturer can provide. While it may be tempting to choose the lowest-cost option, this approach can often lead to higher costs in the long run due to issues such as poor quality, delays, or increased maintenance requirements.
Comparing Quotes from Different Companies
When evaluating potential manufacturers, it’s essential to obtain detailed quotes from multiple companies to compare costs. These quotes should include all relevant expenses, such as mold design and fabrication, production costs, shipping, and any additional services such as quality control or post-production finishing.
However, it’s important to remember that the lowest quote may not always represent the best value. A higher-priced manufacturer may offer superior quality, better customer service, or more advanced capabilities, all of which can result in a more successful project overall.
When comparing quotes, consider the total cost of ownership (TCO), which includes not just the upfront costs, but also ongoing expenses such as mold maintenance, part rework, and potential downtime due to defects or delays.
Importance of Not Compromising Quality for Cost
In the automotive industry, where safety and reliability are paramount, compromising on quality to save costs can have serious consequences. Poor-quality parts can lead to product recalls, warranty claims, and damage to your brand’s reputation, all of which can be far more costly than investing in a high-quality manufacturer from the outset.
Therefore, it’s essential to prioritize quality and reliability when selecting a plastic parts manufacturer. This may mean choosing a company with a higher upfront cost, but one that offers superior quality control, advanced technology, and a proven track record of success.
Payment Terms and Conditions
In addition to the overall cost, it’s important to consider the payment terms and conditions offered by the manufacturer. These terms can have a significant impact on your cash flow and the financial feasibility of the project.
Typical Payment Structures
Payment structures can vary depending on the manufacturer and the specific terms of the contract. Common payment structures include:
- Upfront Payment: A portion of the total cost is paid upfront, often to cover the cost of mold design and fabrication. The remaining balance is paid upon completion of the project.
- Milestone Payments: Payments are made at specific milestones throughout the project, such as after mold completion, after the first production run, and upon final delivery.
- Payment Upon Delivery: The total cost is paid upon delivery of the finished parts.
Each payment structure has its own advantages and disadvantages, and the best option will depend on your specific financial situation and the terms offered by the manufacturer.
Negotiation Tips for Favorable Terms
When negotiating payment terms, it’s important to be clear about your expectations and to discuss any concerns with the manufacturer upfront. Some tips for negotiating favorable terms include:
- Requesting Flexible Payment Schedules: If cash flow is a concern, ask if the manufacturer is willing to offer a more flexible payment schedule, such as spreading payments over a longer period or aligning payments with your production schedule.
- Discussing Discounts for Early Payment: Some manufacturers may offer discounts for early payment or for committing to a long-term partnership. This can be a good way to reduce overall costs while also building a stronger relationship with the manufacturer.
- Clarifying Terms for Changes or Delays: Make sure that the contract clearly outlines the terms for any changes to the project, such as design modifications or delays. This will help avoid disputes and ensure that both parties are on the same page.
In summary, while cost is an important consideration, it’s essential to look beyond the upfront price and consider the long-term value that a manufacturer can provide. By choosing a manufacturer that offers high quality, reliability, and flexible payment terms, you can ensure that your project is successful and cost-effective.
Communication and Customer Service
Ease of Communication
Effective communication is essential for a successful partnership with a plastic parts manufacturer. Clear, consistent, and responsive communication ensures that your project runs smoothly, and any issues that arise are addressed quickly and efficiently.
Importance of Clear and Responsive Communication
From the initial consultation to the final delivery, clear communication is key to ensuring that your requirements are understood and met. A manufacturer that is easy to contact, responsive to inquiries, and proactive in providing updates will give you confidence that your project is in good hands.
When evaluating potential manufacturers, pay attention to how they communicate during the initial stages of the project. Are they quick to respond to your inquiries? Do they provide clear and detailed information about their capabilities and processes? Are they willing to listen to your concerns and provide solutions?
Effective communication is also important for addressing any issues that arise during the project. Whether it’s a design change, a production delay, or a quality concern, a manufacturer that communicates openly and honestly will be better equipped to resolve the issue quickly and minimize its impact on the project.
Availability of Dedicated Project Managers or Customer Support
Having a dedicated project manager or customer support representative can significantly improve the communication process. A project manager serves as your primary point of contact throughout the project, coordinating all aspects of production, from design and tooling to manufacturing and delivery.
A dedicated project manager ensures that your project receives the attention it deserves and that any issues are addressed promptly. They can also provide regular updates on the progress of the project, giving you peace of mind that everything is on track.
When choosing a plastic parts manufacturer, ask if they offer dedicated project management services and inquire about the experience and qualifications of their project managers. A skilled project manager can make a significant difference in the success of your project.
After-Sales Support
The relationship with your plastic parts manufacturer doesn’t end when the parts are delivered. After-sales support is an important aspect of the overall service, ensuring that any post-production issues are resolved and that you are satisfied with the final product.
Warranty and Post-Production Services
Many manufacturers offer warranties on their molds and parts, providing assurance that they stand behind the quality of their work. A warranty typically covers defects in materials or workmanship and may include repair or replacement of defective parts.
In addition to warranties, consider what other post-production services the manufacturer offers. For example, some manufacturers provide ongoing maintenance services for the molds, ensuring that they remain in good condition and continue to produce high-quality parts.
Other post-production services may include assembly, packaging, and logistics support. These services can add value to the partnership by simplifying your supply chain and reducing the need for additional vendors.
Handling of Complaints and Feedback
No matter how well a project is planned, issues can sometimes arise. How a manufacturer handles complaints and feedback is a good indicator of their commitment to customer satisfaction.
When evaluating potential manufacturers, ask about their process for handling complaints. Do they have a formal procedure in place for addressing issues? How quickly do they respond to complaints, and what steps do they take to resolve them?
A manufacturer that is committed to customer satisfaction will take complaints seriously and work diligently to resolve them. They will also value your feedback and use it as an opportunity to improve their processes and services.
In conclusion, effective communication and strong customer service are essential for a successful partnership with a plastic parts manufacturer. By choosing a manufacturer that prioritizes clear communication, provides dedicated project management, and offers comprehensive after-sales support, you can ensure that your project runs smoothly and that you are satisfied with the final results.
Visiting the Facility
Importance of On-Site Visits
Visiting a manufacturer’s facility in person can provide valuable insights into their operations, capabilities, and overall quality. An on-site visit allows you to see the manufacturing process firsthand, ask questions, and assess whether the manufacturer is a good fit for your project.
What to Look For During a Factory Tour
During a factory tour, there are several key areas to focus on:
- Production Area: Observe the cleanliness, organization, and efficiency of the production area. Are the machines well-maintained and operating smoothly? Is the production flow organized and efficient?
- Quality Control Area: Take note of the quality control processes in place. Are parts being inspected at various stages of production? What equipment is being used for quality control, and how are defects handled?
- Tooling and Mold-Making Area: If possible, visit the tooling and mold-making area. This will give you a sense of the manufacturer’s capabilities in designing and fabricating high-quality molds.
- Storage and Inventory Area: Assess how raw materials and finished parts are stored. Are materials being stored in a way that prevents damage or contamination? Is the inventory management system organized and efficient?
During the tour, don’t hesitate to ask questions about the processes you observe. A good manufacturer will be transparent and willing to provide detailed explanations of their operations.
Questions to Ask During Your Visit
An on-site visit is also an opportunity to ask questions and gather more information about the manufacturer’s capabilities and services. Some questions to consider include:
- What are your lead times for mold design and production?
- How do you handle quality control, and what certifications do you have?
- What is your approach to mold maintenance and repair?
- How do you manage production capacity during periods of high demand?
- Can you provide examples of similar projects you have completed?
These questions will help you assess whether the manufacturer has the capabilities and resources to meet your specific needs.
Evaluating the Facility’s Organization and Cleanliness
The organization and cleanliness of a manufacturing facility are often indicators of the company’s overall quality and attention to detail. A well-organized and clean facility is more likely to produce high-quality parts and maintain efficient operations.
Indicators of a Well-Managed Production Environment
A well-managed production environment will be clean, organized, and free of clutter. Machines should be well-maintained and operating smoothly, and there should be clear processes in place for managing production flow and quality control.
In addition to cleanliness, look for signs of efficient production management, such as:
- Clear Signage: There should be clear signage indicating different areas of the facility, such as production, quality control, and storage. This helps ensure that processes are organized and that workers know where to go for specific tasks.
- Lean Manufacturing Practices: Many high-quality manufacturers implement lean manufacturing practices to reduce waste, improve efficiency, and increase quality. Look for evidence of these practices, such as visual management boards, standardized workstations, and continuous improvement initiatives.
- Safety Measures: A safe working environment is a sign of a well-managed facility. Look for safety measures such as proper protective equipment, clearly marked emergency exits, and well-maintained safety equipment.
Observing Safety and Workflow Efficiency
During your visit, pay attention to how the workflow is managed. Are workers moving efficiently between tasks? Are materials and parts being handled in a way that minimizes the risk of damage or contamination? Are safety measures being followed consistently?
A facility that prioritizes safety and workflow efficiency is more likely to produce high-quality parts and deliver projects on time. It also indicates that the manufacturer values the well-being of their employees, which can be a good sign of a positive company culture.
In summary, an on-site visit to a plastic parts manufacturer’s facility can provide valuable insights into their operations, quality control processes, and overall management. By observing the production environment and asking the right questions, you can assess whether the manufacturer is a good fit for your project and whether they have the capabilities to meet your needs.
Sustainability and Environmental Responsibility
Green Manufacturing Practices
As environmental concerns continue to grow, sustainability has become an increasingly important consideration in the automotive industry. Choosing a plastic parts manufacturer that prioritizes green manufacturing practices can help reduce your project’s environmental impact and align with your company’s sustainability goals.
Company’s Commitment to Reducing Environmental Impact
When evaluating potential manufacturers, inquire about their commitment to reducing environmental impact. This can include practices such as:
- Energy-Efficient Production: Manufacturers that use energy-efficient machinery and processes can reduce their carbon footprint and lower energy costs. Ask about the manufacturer’s energy consumption and whether they have implemented any energy-saving initiatives.
- Waste Reduction: Reducing waste is a key component of sustainable manufacturing. Look for manufacturers that have implemented waste reduction programs, such as recycling scrap materials, minimizing excess inventory, and reducing packaging waste.
- Sustainable Materials: Some manufacturers offer the option to use sustainable or recycled materials in their production processes. This can help reduce the environmental impact of your project and contribute to a circular economy.
By choosing a manufacturer with a strong commitment to sustainability, you can ensure that your project aligns with your company’s environmental goals and contributes to a more sustainable future.
Use of Recycled Materials or Sustainable Practices
One of the most effective ways to reduce the environmental impact of plastic parts production is by using recycled materials. Many plastic parts can be made from recycled resins, which reduces the demand for virgin materials and minimizes waste.
In addition to using recycled materials, some manufacturers implement other sustainable practices, such as:
- Closed-Loop Recycling: In a closed-loop recycling system, scrap materials from the production process are collected, reprocessed, and used to produce new parts. This reduces waste and conserves resources.
- Water Conservation: Injection molding requires the use of water for cooling, and some manufacturers have implemented water conservation measures to reduce their water usage. This can include using closed-loop cooling systems or recycling wastewater.
- Eco-Friendly Packaging: Sustainable manufacturers often use eco-friendly packaging materials, such as recycled cardboard or biodegradable plastics, to reduce the environmental impact of shipping and distribution.
When evaluating potential manufacturers, ask about their use of recycled materials and other sustainable practices. Choosing a manufacturer with a strong commitment to sustainability can help you meet your environmental goals and reduce the overall impact of your project.
Compliance with Environmental Regulations
Compliance with environmental regulations is a critical aspect of sustainability, particularly in the automotive industry, where strict environmental standards must be met. A manufacturer that adheres to these regulations demonstrates their commitment to environmental responsibility and reduces the risk of legal or regulatory issues.
Certifications and Adherence to Environmental Standards
When choosing a plastic parts manufacturer, inquire about their compliance with environmental regulations and whether they hold any relevant certifications, such as ISO 14001. ISO 14001 is an internationally recognized standard for environmental management systems, and certification indicates that the manufacturer has implemented effective processes for managing their environmental impact.
In addition to ISO 14001, consider whether the manufacturer adheres to other environmental standards, such as the European Union’s REACH (Registration, Evaluation, Authorization, and Restriction of Chemicals) regulation or the United States Environmental Protection Agency (EPA) regulations.
Waste Management and Energy Efficiency Measures
Effective waste management is another important aspect of environmental responsibility. A manufacturer with a strong waste management program will have processes in place to minimize waste, recycle materials, and dispose of hazardous waste safely and responsibly.
Energy efficiency is also a key consideration. Manufacturers that implement energy-saving measures, such as using energy-efficient machinery, optimizing production processes, and reducing energy consumption, can significantly reduce their environmental impact.
When evaluating potential manufacturers, ask about their waste management and energy efficiency measures. A manufacturer that prioritizes environmental responsibility will have established processes in place to manage their environmental impact and ensure compliance with relevant regulations.
In conclusion, sustainability and environmental responsibility are important considerations when choosing a plastic parts manufacturer for your automotive project. By selecting a manufacturer that prioritizes green manufacturing practices, uses recycled materials, and complies with environmental regulations, you can reduce the environmental impact of your project and contribute to a more sustainable future.
Making the Final Decision
Comparing Your Shortlist
After evaluating potential plastic parts manufacturers based on the factors discussed in this guide, the next step is to compare your shortlist and make a final decision. This involves carefully weighing the pros and cons of each manufacturer to determine which one is the best fit for your project.
Creating a Comparison Matrix for Key Criteria
One effective way to compare your shortlist of manufacturers is by creating a comparison matrix. This matrix should include key criteria such as:
- Experience and Expertise: How experienced is the manufacturer in the automotive industry? Do they have a proven track record of success with similar projects?
- Technical Capabilities: Does the manufacturer have the machinery, technology, and expertise needed to produce your parts to the required specifications?
- Quality Control: What quality control measures are in place, and do they have the necessary certifications?
- Production Capacity: Can the manufacturer meet your required production volumes within your specified timeline?
- Cost: How do the manufacturer’s costs compare, and what is the total cost of ownership?
- Location and Logistics: How will the manufacturer’s location impact shipping costs and lead times?
- Communication and Customer Service: Is the manufacturer easy to communicate with, and do they offer strong customer support?
- Sustainability: Does the manufacturer prioritize sustainability and environmental responsibility?
By assigning scores to each criterion, you can objectively compare the manufacturers and identify the one that best meets your needs.
How to Weigh Different Factors According to Your Priorities
While all of the criteria discussed in this guide are important, some may be more critical to your specific project than others. For example, if you are working on a tight deadline, production capacity and lead times may be your top priorities. If sustainability is a key concern, you may place more weight on the manufacturer’s environmental practices.
When making your final decision, consider how each criterion aligns with your overall project goals and priorities. It’s also important to consider the long-term implications of your choice, such as the potential for a long-term partnership or the impact on your company’s reputation.
Negotiating the Contract
Once you have selected a plastic parts manufacturer, the final step is to negotiate the contract. This contract should clearly outline the terms and conditions of the partnership, including pricing, production schedules, quality requirements, and payment terms.
Key Elements to Include in the Contract
When negotiating the contract, be sure to include the following key elements:
- Scope of Work: Clearly define the scope of the project, including the parts to be produced, the materials to be used, and any specific requirements or standards that must be met.
- Pricing and Payment Terms: Outline the total cost of the project, including any additional fees for mold maintenance, shipping, or post-production services. Specify the payment structure and schedule, including any milestones or deadlines.
- Production Schedule: Include a detailed production schedule, with deadlines for each stage of the project, from mold design and fabrication to final delivery. Specify the consequences of missed deadlines or delays.
- Quality Requirements: Define the quality standards that must be met, including any specific testing or inspection processes. Include provisions for handling defects or non-conforming parts.
- Warranties and After-Sales Support: Specify any warranties on the molds or parts, as well as the terms for after-sales support, such as mold maintenance or repair services.
- Confidentiality and Intellectual Property: Include provisions to protect your intellectual property, as well as any confidentiality agreements needed to safeguard proprietary information.
Importance of Clear Terms on Quality, Delivery, and Payments
Clear and detailed contract terms are essential for ensuring that both parties understand their obligations and expectations. By outlining the terms for quality, delivery, and payments, you can reduce the risk of disputes and ensure that the project runs smoothly.
When negotiating the contract, be sure to discuss any concerns or questions with the manufacturer and reach a mutual agreement on all terms. A well-negotiated contract will provide a strong foundation for a successful partnership and ensure that your project is completed to your satisfaction.
Conclusion
Recap of Key Takeaways
Choosing the right automotive plastic injection molding company is a critical decision that can have a significant impact on the success of your project. By carefully evaluating potential manufacturers based on factors such as experience, technical capabilities, quality control, production capacity, cost, and sustainability, you can make an informed decision that aligns with your project goals and priorities.
Final Thoughts
Investing the time and effort to select a reliable and experienced plastic parts manufacturer will pay off in the long run, ensuring that your parts are produced to the highest standards and delivered on time. By prioritizing quality, communication, and environmental responsibility, you can build a strong and successful partnership that supports the success of your automotive project.
Additional Resources
Links to Relevant Articles or Guides
For further reading on plastic injection molding processes and best practices, consider exploring the following resources:
- Understanding Injection Molding: A Comprehensive Guide
- Choosing the Right Materials for Automotive Plastic Parts
- Optimizing Mold Design for High-Quality Production
Contact Information for Further Consultation
If you have any questions or would like personalized advice on selecting a plastic parts manufacturer for your automotive project, please feel free to reach out to us at [contact information]. We are here to help you navigate the process and ensure the success of your project.